PROJECTS
PDF Bi-Pedal Research Robot
System Overview
The Olin College robot had twelve control axis, with twelve high power motor amplifiers, twelve encoder channels and twelve potentiometer interfaces. The system required a variety of other interfaces to switches, strain gauges, accelerometers, gyroscopes and other sensors. Commercially available hardware lacked the necessary safety features, channel density, and throughput. Using PC/104 boards would need half a dozen boards and still require custom external circuitry.
Bolton Engineering implemented a low-latency Firewire based system that allowed a tethered computer to control the robot with a 2KHz update rate with less than 250uS latency, more than sufficient to intricately model and control balance and movement. The system was implemented as a multi-board set.
Power Control Board
The original robot design was difficult to power-up and debug. The large number of motors and amplifiers presented essentially a short-circuit to the high power 48V system power supply. Bolton Engineering Inc implemented two eight-channel power sequencing cards to limit system inrush current and to act as circuit breakers in the event of catastrophic system failures. Each motor amplifier had its own sequencer and current-limiting circuitry. Having these boards greatly simplified the system wiring and made the system much more stable during subsequent development.
Firewire, Analog and Digital I/O Card
The Robot required two Analog and Digital I/O cards to control all axis. Each card included six motor amplifier D/A converters and interfaces, six motor encoder interfaces, twenty-four general-purpose configurable instrumentation amplifier analog interfaces and A/D converters, and twenty-four general purpose digital inputs. All I/O incorporated ESD and EMI protection.
The Firewire link was controlled using an 8031 processor. A Texas Instruments (TI) Link Controller and PHY chip implemented the Firewire interface. An Intel/Altera Cyclone FPGA implemented the many on-board registers, a high speed link to the Firewire controller, the motor encoder interfaces, and a variety of safety features. A Firewire pass-through port was implemented so that the Firewire connection could be daisy-chained and only one Firewire cable needed to be run between the Robot and the control PC.
Project Scope
Bolton Engineering designed all schematics, the circuit boards, wrote and simulated all hardware in Intel/Altera Cyclone FPGAs, wrote all documentation, constructed the boards, wrote the embedded Firewire software in ‘C’ and Linux Firewire driver code.
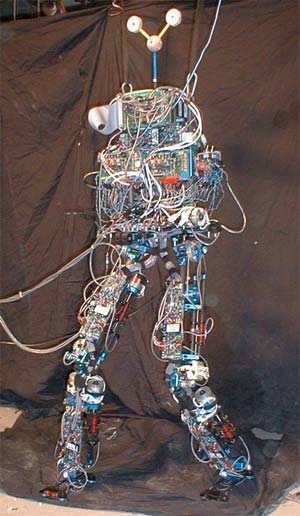
Professor Gill Pratt at Franklin W. Olin College of Engineering hired Bolton Engineering, Inc. to develop a custom high-speed, low-latency interface between his multi-axis bi-pedal robot, and a control computer. Bolton Engineering constructed three boards to replace student-designed boards that had proven to be noisy and unreliable.